Industry Activities
Born for Low Carbon Emission, KING YUAN DAR Multifunctional Sintering Furnace Accelerates Customers’ Industrial Upgrade
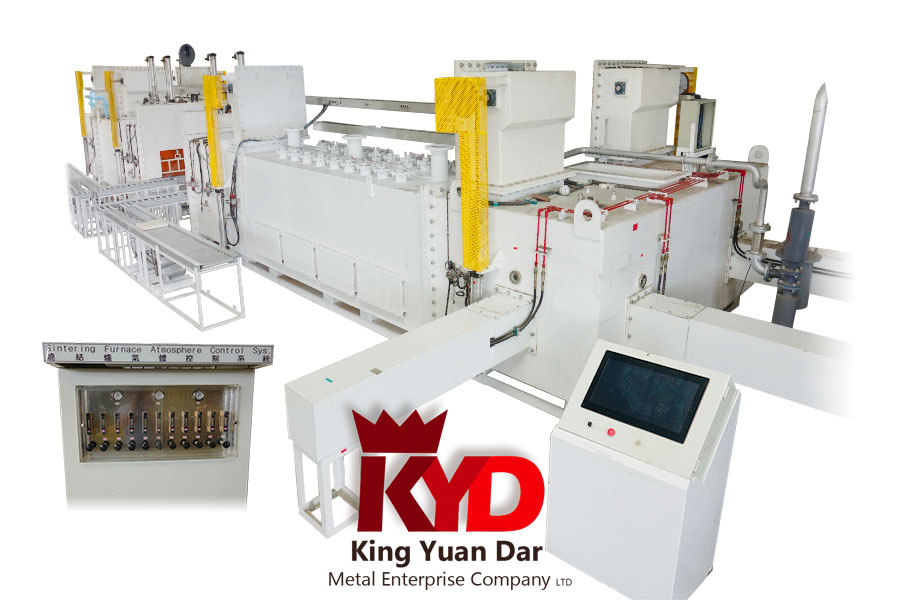

Add to my favorite
2024-02-19
King Yuan Dar Metal Enterprise Co., Ltd. ("KYD") with adequate heat treatment R&D technology and equipment manufacturing experience has been serving customers in the global fasteners, parts and powder metallurgy industries with heat treatment needs for nearly 30 years, and has released a number of eye-catching and innovative products responding to actual industrial needs, including the AI Continuous Batch Green Chamber Furnace and Vacuum Continuous Cyclic Energy Saving Spheroidizing Furnace, both of which have been granted international patents, creating a competitive niche in the international market for its customers. In H2 2023, in response to the global trend of energy saving and carbon reduction, KYD further released the new "Cyclic Continuous Vacuum High-Temperature Sintering Furnace", integrating various excellent features that allow users to streamline production and achieve superior product quality.
Eco-friendly AI Intelligent System
The introduction of heat treatment equipment with multiple intelligent functions that meets the concept of green & sustainable development is a main trend of the industrial application, so the new equipment developed by the team of KYD General Manager Chang Lung Tseng has integrated many relevant features in the operating system, including: an intelligent hardware interface allowing on-site personnel to operate it by only setting material feeding values; AI remote image monitoring to alert the operator of temperature abnormalities in a timely manner; voltage stabilization to maintain normal operation; the gas ratio in the machine being properly adjusted to improve the yield of workpieces; heat generated from manufacturing being recycled and reused through conduction/convection/radiation to further reduce power consumption; and hydraulic push-and-feed improving productivity and stabilizing production quality.
It is understood that the core heat treatment technology of KYD's new sintering furnace is highly innovative among similar products in the current market. "Starting from Taiwan and aiming to expand globally, KYD hopes to draw more customers' attention to the advantages that its equipment can bring to their applications,” said General Manager Tseng.
Patents Approved in Many Countries; Comprehensive Heat Treatment Equipment Integration Solutions
The oxidation furnace structures, chamber furnace structures and heat recovery systems KYD developed have been patented in Taiwan, China, Germany and the U.S., and the in-house process management is fully compliant with the ISO 9001 and IATF 16949 requirements. In addition, KYD continues to focus on the R&D of environmentally-friendly AI heat treatment equipment and provides comprehensive solutions that integrate heat treatment processing, gas supply, and equipment manufacturing. KYD maintains long-term cooperation with not only fastener customers, but also many others in the automotive and motorcycle industries, as well as government agencies.
"My long-term goal is to enter the U.S. heat treatment market within two years, and then return to Taiwan from overseas to gain a higher market share for KYD's competitive equipment," said General Manager Tseng.
It is expected that with the complementary integration of the existing plant in Luchu (Kaohsiung) and the Changbin plant and the Thailand plant under construction close to the supply chain of automobile factories, KYD will continue to expand its global market in 2024 and provide more complete one-stop services for heat treatment equipment to customers.
Contact: General Manager Chang Lung Tseng
E-mail: gold.dollar@msa.hinet.net
金元達
循環連續式真空高溫燒結爐
熱處理
扣件
零組件
粉末冶金
減碳
AI
環保
節能
King Yuan Dar Metal Enterprise
KYD
Cyclic Continuous Vacuum High-Temperature Sintering Furnace
heat treatment
fastener
component
powder metallurgy
carbon reduction
environmental protection
energy saving
扣件
國際展會
惠達雜誌
匯達實業
外銷媒合
廣告刊登
螺絲五金
五金工具
紧固件
台灣扣件展
印度新德里螺絲展
越南河內螺絲展
墨西哥瓜達拉哈拉螺絲展
美國拉斯維加斯螺絲暨機械設備展
波蘭克拉科夫螺絲展
義大利米蘭螺絲展
德國司徒加特螺絲展
wire Dusseldorf
FASTENER FAIR INDIA
FASTENER FAIR VIETNAM
FASTENER FAIR MEXICO
FASTENER POLAND
FASTENER FAIR ITALY
FASTENER FAIR GLOBAL
FASTENER WORLD
READ NEXT
Industry Activities
2024-03-20

Subscribe
