BI-MIRTH: Strengthening the Foundation of Chipboard Screws
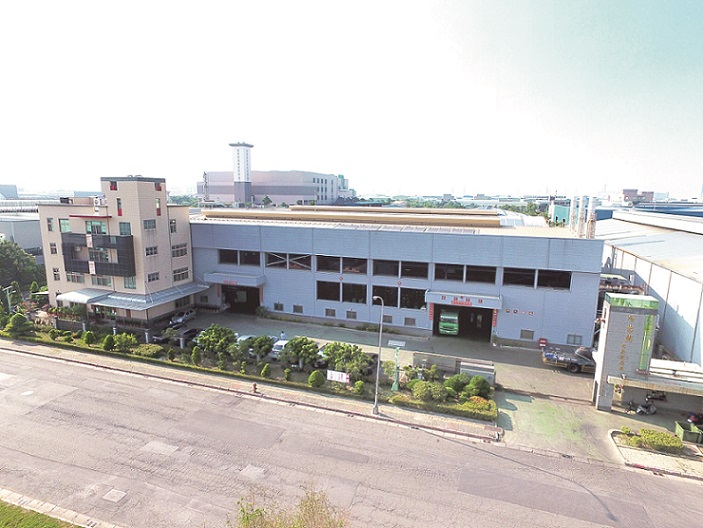
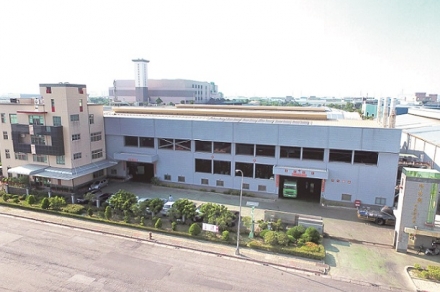
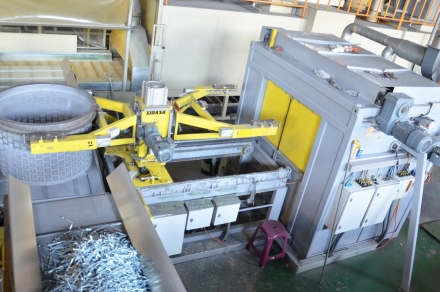
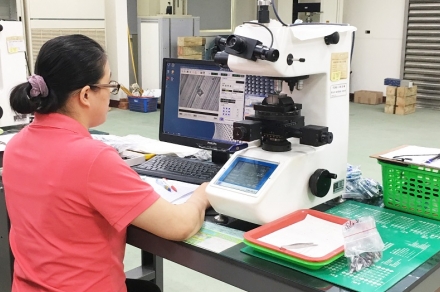
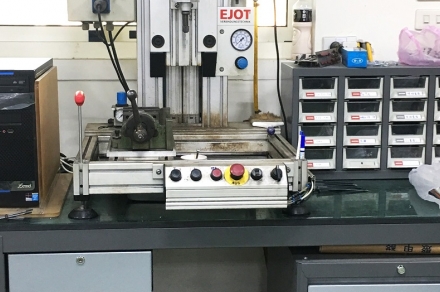
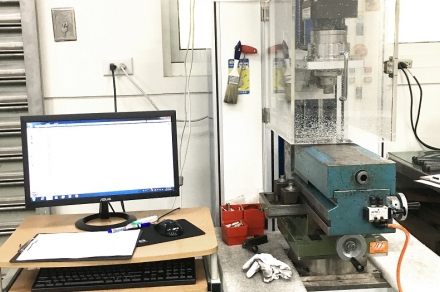
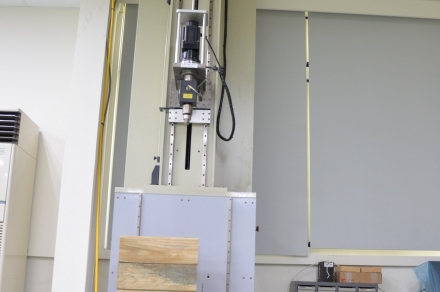
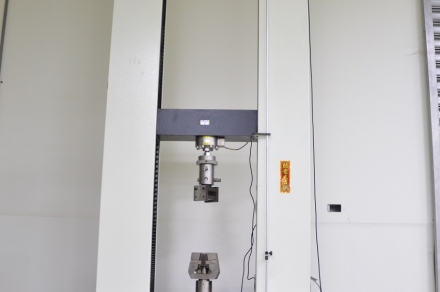
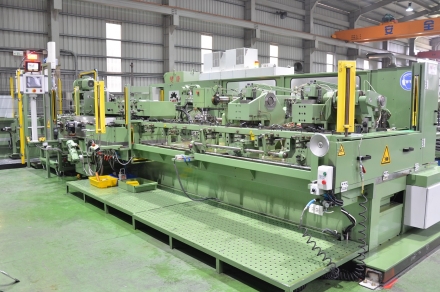

Founded in 1986, Bi-Mirth Corporation just celebrated the 30th anniversary of its establishment. The company currently has four plants for screw manufacturing, electroplating, coating and packaging, along with an accounting office located in Taichung. The company prides itself for its quality and has received ISO9001, TSI6949, ISO14001, ETA, ICC certifications. As the market becomes more competitive, it is necessary for Bi-Mirth to find an edge to strive in the fastener industry.
Updated and Upgraded
Bi-Mirth has its own facilities for manufacturing, electroplating, coating, and packaging. However, the company is also dedicated to continuous growth and improvement, which is why a new 3-in-1 machine along with a mechanical arm that arrived its manufacturing plant on June 2017. On top of that, two of the older machines were modified so that they could accommodate their respective mechanical arm for future production. This increases efficiency and decreases the chances of human error.
Emphasis has also been placed in surface treatment, as Bi-Mirth opened its brand new coating facility at the Benzhou Industrial Park. Two coating machines manufactured by SIDASA from Spain were imported about a year ago in order to provide a more consistent finish for the end product. The chance of “recess fill” is drastically reduced with the machines’ precision while not compromising the corrosion resistance required for the screws. Bi-Mirth is also planning to import another machine from SIDASA in order to prevent capacity overload while maintaining their standards.
A specialized laboratory with equipment such as Atomic Absoportion Spectroscopy (AAS), X-Ray Thickness Analyzer, and Automatic Titrator were installed for quality assurance. The main goal for Bi-Mirth’s coating facilities now is to achieve higher corrosion resistance for SST and Kesternich Cycles with lower thickness in order to be more competitive in the market. The current achievable range goes from 1,000 – 2,000 SST hours and 15 – 30 Kesternich Cycles.
Market and Client Differentiation
Bi-Mirth produces nearly 800 tons of screws per month and these products are mainly exported to Europe (70%), USA (25%) and other countries (5%). The company is actively reaching to emerging markets “BRICs” and the initiative “One Belt, One Road” to expand to new markets. Besides establishing a stable quality, the essence is to understand what different markets need. For instance, Japanese customers are a lot more meticulous compared to clients from other countries, and they also tend to troubleshoot issues in an alternative way. Interacting with people from different cultures gives Bi-Mirth an opportunity to learn. The next market that the company wants to tackle is the Middle East since it is growing exponential. However, the most important factor for the company is to maintain its standard despite satisfying the demands for different markets.
Reacting to Environmental Changes
The effects of global warming have been consistently spiraling for the past few decades. One of the main impacts for the fastener industry caused by such phenomenon is a demand for higher corrosion resistance to combat drastic climate change. Fasteners in different regions require specific certification, such as the C4 for Scandinavian countries. The extreme temperature changes in the Nordic countries make it crucial for them to withhold high standards for surface treatment. Acidic rain is one of the aftermaths of climate change, and to combat that, wood gets treated with ACQ technology to further protect fasteners from rust and oxidation. Rust resistance is crucial for wood screws, which is why Bi-Mirth has not only applied for ETA and ICC, but also C4 for their coating. Another ongoing project for the company is the development of screws that can be used at harsher climates and temperatures without signs of hydrogen embrittlement or fracture.
■ Sustaining and Improving
As the market gets more competitive, a lot of manufacturers are undergoing transformation from standard fastener production to more specialized products to cater to auto and aerospace supply chains. Other than Bi-Mirth’s surface treatment plant that provides electroplating services for other suppliers, the company is still putting their focus and expertise on construction fasteners. The main reason for this is because Bi-Mirth wants to focus on what the company has been doing for so long. The expertise and experience within this type of screws is how Bi-Mirth stayed and will continue to stay in the industry.
» Contact: Manager Tom Shih E-mail: sales@bimirth.com.tw

Subscribe
