GOVERNMENTS/ASSOCIATIONS/FASTENER GROUPS
Interview with NFDA President Jim Degnan
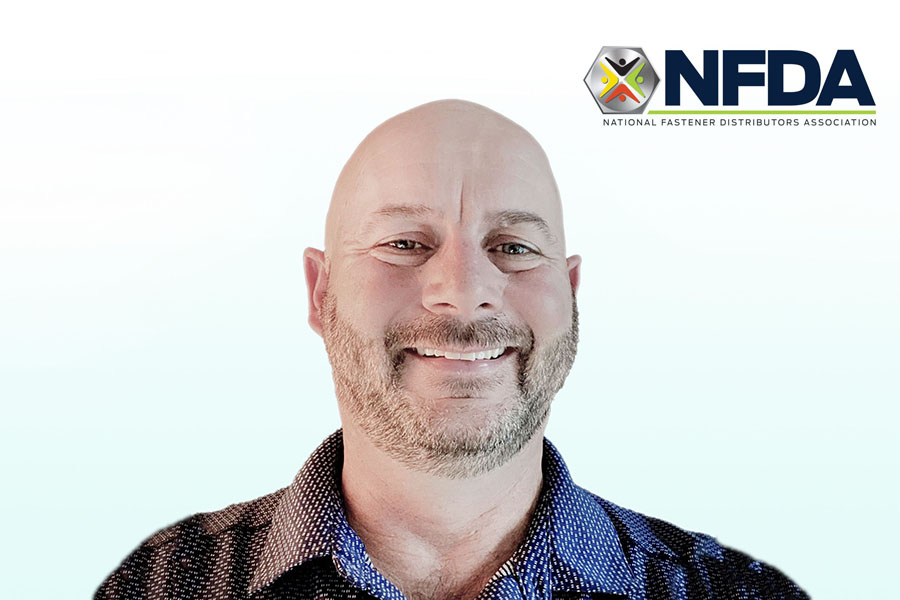

Add to my favorite
2023-11-21
With inventory, freight cost, and inflation continuing to impact the global supply chain since 2022 (and the U.S. industry is no exception), do you think the pressures on the U.S. fastener industry due to these issues have eased this year, and are there any new emerging issues that are worth paying attention to?
A: While freight costs and lead times have improved, inflation continues to have a large impact on our industry. Many production costs including labor and inventory carrying costs have increased. The availability of qualified labor is also a frequent topic of conversation. Recruiting, training, and retaining employees is more critical now than ever.
(Following Q1) Which of these issues do you consider to be the highest priority for the U.S. fastener industry to deal with at this stage? Why?
A: I believe that the highest short-term priority will be managing costs as inflation continues to impact many product classes and industries. Even with the efforts of the US government to slow it down through increased interest rates, inflation continues to affect all aspects of our industry. Also, any significant economic downturn will just increase the complexity of managing changing costs. However, skilled labor availability will be the larger, longer-term issue that companies must be addressing now.
The practices adopted by U.S. fastener distributors in response to changes in market supply & demand and industrial upgrading have always been a model for their counterparts in other countries to learn from. In the face of these old and new challenges in the market that we are all closely concerned about, how do the U.S. distributors, who stand on the front line as the gatekeepers for their customers, cope with and overcome them? Do you have any practical examples to share?
A: The volatility of the fastener market over the last several years has motivated US distributors to expand investment in data analytics, standardization, supply chain visibility, and system technologies to help with these new market dynamics. But none of that will have a material impact without encouraging your employees to empathize with your customers, clearly understand their requirements, and empowering them to solve problems directly. Our industry employs some of the best and brightest folks. They are the key to our success.
Under the framework of the new U.S.-Mexico-Canada Trade Agreement (USMCA) and with the advantage of preferential tariffs and geographic location, it is reported that some U.S. fastener companies are also investing in Mexico to set up their factories. Do you think that this trend will cause some subtle changes to the existing U.S. fastener distribution system?
A: We have all heard the quote: “The only constant in life is change”. And that applies to the US fastener distribution industry more than most. Our industry has always worked effectively through the perpetual changes in our marketplace. Our world is dynamic, and we must move with it or deal with consequences. The trend of U.S. fastener companies investing in Mexico to set up factories under the USMCA framework is indeed a topic of considerable interest. With labor shortages in the U.S., the proximity of Mexico and their strong labor force is an attractive destination. While automotive and electronic manufacturing have long been established in Mexico, we're now witnessing many other manufacturing segments exploring this option. Our industry has years of experience serving the companies already in Mexico, and in many other countries.
According to the latest U.S. Customs statistics, the U.S. imported about US$3.8 billion of fasteners in the first 7 months of 2023, with the top 3 import origins being Taiwan, China and Japan. As far as you know, what are the main applications for the fasteners the U.S. imported from these three countries? And, what advantages do fasteners from these three countries respectively present to U.S. fastener distributors? Are there any new trends in fastener manufacturing and development in the U.S.?
A: Fastener imports from Taiwan, China and Japan are used across a very wide range of applications in industries including construction, automotive, consumer electronics, and machinery manufacturing to name just a few. The appeal of these fasteners is primarily their cost. Many commodity fasteners can only be purchased in volume from overseas manufacturers. There are also many US fastener manufacturers who have opened manufacturing locations in Asia to expand their production capacity and to serve the local markets.
In the first 7 months of this year, more than 35% of U.S. fastener imports (about 320,000 tons) came from Taiwan, a much higher percentage than China and Japan, showing that Taiwan and the U.S. fastener industry have been cooperating extraordinarily closely. What do you think are the reasons that the supply chain between Taiwan and the U.S. has remained close over the years?
A: The close collaboration between Taiwan and the U.S. fastener industry is rooted in longstanding relationships built on quality, pricing, reliability, and consistent delivery performance. These foundational pillars have been nurtured over time, resulting in robust and enduring supply chain partnerships. While the U.S. fastener industry is always exploring opportunities to expand its vendor base, Taiwan's reputation for excellence and dependability has made it a preferred partner for U.S. distributors. As we explore global options, other countries like Malaysia, India, and Turkey offer unique strengths for various product lines, providing diversification opportunities within the supply chain.
With the trial implementation of the EU's CBAM measures from October 1 this year, fastener manufacturers in Taiwan, China, and many other Asian countries have begun to actively introduce the concept of "energy saving and carbon reduction" in all aspects to strengthen their competitiveness. Will low carbon fasteners also become a requirement for upstream suppliers of U.S. fastener distributors in the near future?
A: With the upcoming trial implementation of the EU's CBAM measures, many fastener manufacturers in Asia, including Taiwan and China, are proactively embracing "energy-saving and carbon-reduction" principles to enhance their competitiveness. The adoption of low-carbon fasteners may indeed become a future requirement for upstream suppliers of U.S. fastener distributors. We have witnessed similar trends with the trickle-down effect of various industry initiatives. As we await the finalization and potential modifications of CBAM requirements in the coming weeks and months, it is possible that carbon reduction measures will be integrated into the broader spectrum of our industry practices in the U.S.
As the new president of NFDA, have you set a few goals to achieve during your term?
A: The NFDA board has established several strategic objectives, mostly around the improvement of membership value. Our objectives cover a range of topics including employee development, recruiting, training, mentoring, and effective networking practices. We are always committed to helping our members thrive in a global marketplace.
What NFDA events have been planned for the upcoming year? Will there be any exchange event with other national fastener associations or industries?
A: We have several events scheduled for the upcoming year including:
1. NFDA Virtual Program – November 30, 2023
2. 2023 YFP and NFDA Virtual Holiday Party – December 14, 2023
3. 2024 NFDA Annual Meeting and ESPS – June 12, 2024
4. 2024 NFDA Executive Summit in San Diego, CA – October 16-18, 2024
What are your expectations for the U.S. fastener industry in 2024?
A: The US fastener industry will have some growth challenges in 2024 given the uncertainty of the economy, but US fastener distributors will continue to grow as more of the market recognizes the competitive advantages of working with a strong distribution partner to assist them with the ever-changing dynamics of a global supply chain.
美國扣件經銷商協會
理事長Jim Degnan
螺絲
通膨
台灣供應鏈
美加墨協議
美國扣件經銷商協會
President Jim Degnan
screw
appreciation
Taiwan supply chain
扣件
國際展會
惠達雜誌
匯達實業
外銷媒合
廣告刊登
螺絲五金
五金工具
紧固件
台灣扣件展
印度新德里螺絲展
越南河內螺絲展
墨西哥瓜達拉哈拉螺絲展
美國拉斯維加斯螺絲暨機械設備展
波蘭克拉科夫螺絲展
義大利米蘭螺絲展
德國司徒加特螺絲展
wire Dusseldorf
FASTENER FAIR INDIA
FASTENER FAIR VIETNAM
FASTENER FAIR MEXICO
FASTENER POLAND
FASTENER FAIR ITALY
FASTENER FAIR GLOBAL
FASTENER WORLD
READ NEXT

Subscribe
