News
Multi-station Parts Forming. How Does a Parts Former Differ from a Nut Former?
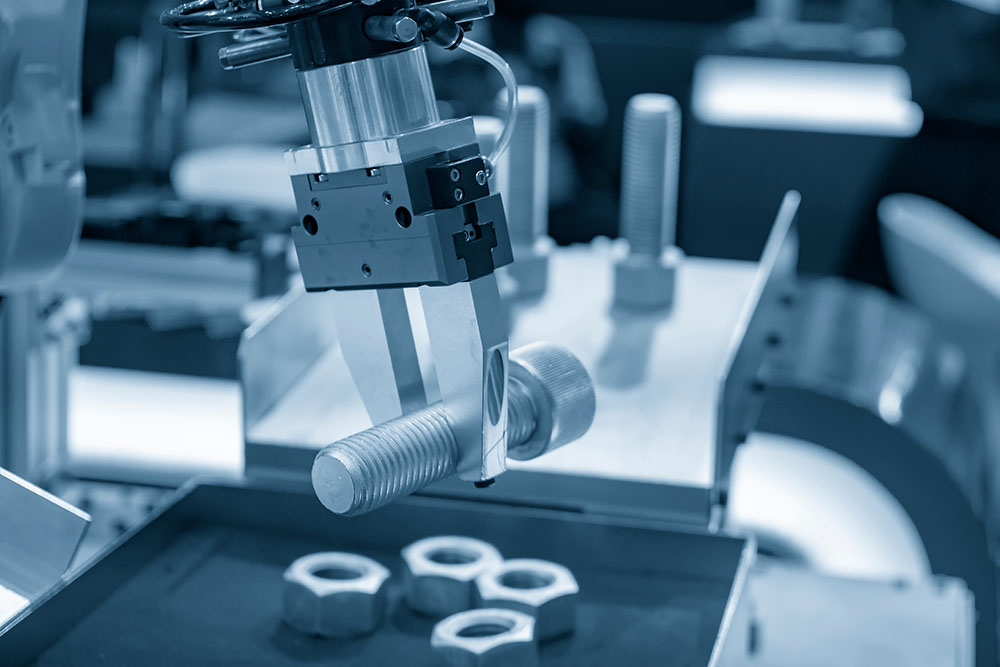

Add to my favorite
2021-11-01
by Laurence Claus
The majority of screws and some bolts are simple configurations that can be formed merely by upsetting a head on a cylindrical body. The one-die-two-blow equipment utilized to make such parts is the simplest available. These machines are ideal for such parts as they are fast and efficient. When parts are more complex, such as many bolts, shoulder screws, special engineered parts, and nuts, the forming equipment must be able to shuttle the part past multiple dies resulting in the ability to strike the part at least three or more times. These machines that are able to accomplish this are known as Multi-station Parts or Nut Formers.
Parts Formers are generally used to make more complex externally threaded parts while Nut Formers are used for internally threaded nuts and hollow parts. Although both Parts and Nut Formers are conceptually similar, there are some differences which lend one to be better suited to specific part designs than the other. This article will explore Multi-station Formers as a general topic but also look at what sets Nut Formers apart from Parts Formers.
What do Multi-station Formers Do?
Prior to considering the machine itself, we should first consider what consumers and manufacturers want from these machines. The answer to this question is pretty simple, consumers want quality parts, suited for the intended purpose at a reasonable price and manufacturers want to provide such parts with the most efficient processes or methods available. In other words, as parts become more complex and sophisticated they usually become more challenging to manufacture. The manufacturer is motivated to remain competitive, and, therefore, must evolve their manufacturing capabilities to be as efficient as possible. Let us consider for example a high volume trimmed hex head part. An untrimmed blank could be manufactured on a simple one-die-two-blow header and transferred to a secondary trimming operation or the part could be manufactured complete on a Multi-station Part Former. The end result is exactly the same, but in the first scenario the blanks have to be collected after heading, moved, and reloaded in the secondary trimmer. The quality of the part should be no different, but additional labor and burden has been added to facilitate the extra handling and operation of a second machine. Although this example may begin to fall apart when the volume begins to decrease, it is still illustrative that there are definite advantages to fully completing parts in one manufacturing process. The process of producing a part in an almost complete form is known as “net shape” manufacturing.
A part is net shape when it comes off the header or former complete except for a thread and any post heat treating or surface finishing steps. A part is considered “near net shape” when it comes off the header or former requiring additional forming steps, such as shaving a groove, undercut, special geometry (like a sphere or ball shape) or squaring a surface (like an underhead bearing surface, flange diameter, or tip end). Often times these secondary operations will be necessary because no manner of header or forming equipment is capable of producing the geometry or tolerances required, although just as often, perhaps, they are required because the manufacturer does not have the multi-station equipment or knowledge how to use the multi-station equipment that would facilitate net shape production.
Although the forming process for fasteners can produce some very interesting and elaborate parts, the fundamental processes available from the machines that make the parts is relatively limited. Headers and formers can essentially perform three different processes:
1. Upsetting > 2. Extrusion > 3. Trimming and Piercing
Upsetting is perhaps the most basic of fastener manufacturing processes. It is the process of accumulating or moving material into a head or collar. For the simplest of screws this is all that is needed. The manufacturer starts with a round cylinder of wire and moves some portion of it into a larger diameter and different geometry head shape. For all practical purposes upsetting is the only thing that the simplest one-die-two-blow headers do.
Extrusion takes several different forms but is essentially the process of moving material either forward or backwards to achieve smaller diameters, special shapes, or hollow features. Parts can include forward extrusion processes known as “Open Extrusion” or “Trapped Extrusion” or reverse extrusion where material flows backwards along a pin.
Trimming can be accomplished on external parts to provide a shaped head or collar. The most common example would be a trimmed hex head fastener. The material is simply sheared into the desired shape. Likewise, an internally threaded or hollow part usually has a web separating the two sides of the hollow feature that must be pierced to provide the through hole.
As parts become more complex they require multiple combinations of these operations to form the part. No longer can the manufacturer just upset the head. Instead, for more sophisticated bolts and externally threaded components, manufacturers may have to employ several forward extrusions and a trimming operation along with the upsetting operation to complete a net shape part. Likewise manufacturers of nuts are likely to incorporate multiple reverse extrusions, upsetting, and a piercing operation to achieve a net shape nut blank. Naturally, this takes more than one forming station to accomplish and can only be realized using multi-station machines.
In addition to providing more than one forming station to conduct this combination of operations, multi-station machines may also be designed with other mechanisms or tools that perform special functions to provide net shape parts. One important mechanism is the “Transfer” or how parts are shuttled from one station to another. In some instances these mechanisms can turn, orient, or introduce blanks into the forming process which may provide versatility regarding which side of the machine the forming process is occurring on or provide a means to introduce the part along a non-traditional axis. Another mechanism might be to introduce a segmented tool, which is really a mechanism that splits the dies open and allows the manufacture of configurations impossible to produce in solid tooling.
Parts and Nut Formers can be designed to run cold or hot. Most Multi-station Formers are cold formers as there is simply a larger demand for such equipment. However, when parts, especially nuts or other hollow parts, start to get larger in size, have very complex geometries, or are being manufactured with exotic, hard to form materials, using a hot former may be advantageous. In most cases where heat is added, it is included in the initial design of the machine, so that heat introduction and control are well regulated. Of course, heat can be a later add-on or introduced prior to entering the machine, but these situations are probably not as optimal as when the machine has been designed to introduce heat into the parts.
What is the Anatomy of a Multi-station Former?
Conceptually a Multi-station Former is set-up much like the simple one-die-two-blow headers except that it has more than one die. Heading machines have two sides in which forming occurs. There is a stationary side of the machine which houses the dies and a moving (sliding) ram that houses the punches (sometimes called hammers) which strike the part forcing it into the die.
One of the signature attributes of a one-die-two-blow machine is that even though it only has a single die, there are two punches or hammers that separately strike the part before it is complete. Although this concept has been adapted to multi-station machines, including 2-die-3-blow headers and 2-die-4-blow headers, machines normally considered to be Multi-station Parts and Nut Formers have one hammer (blow) for each die. In this way, a machine with four dies would be called a 4-die-4-blow header or parts/nut former. In these machines, therefore, every time the machine strokes (comes together) it will be performing the same number of operations as dies and one finished part will be completed.
This process is no different in concept from a part on an assembly line that moves from one station to the next until it is complete. Each stop along the way is only one incremental piece of the entire assembly process. Taking this into account, one of the key factors in the successful operation of a multi-station machine is the transfer mechanism. This mechanism must be able to successfully shuttle the part from one station to the next. This can get tricky. In the analogy above, parts on an assembly line are often shuttled on a fixture or a pallet so that the part actually never moves, only the pallet it is on. If you have to move the part each time, this process gets significantly more difficult because not only do you have to grab the part but re-establish it in the desired orientation. This, however, is what occurs in a multi-station header, i.e. the part is individually moved each time. This adds a layer of complexity including added manufacturing controls to prevent dropping the part or changing its angular orientation and presentation to the next die. The impact of these added controls is normally needing to slow the speed of the machine.
Once the manufacturer gets the order in which the part is to be manufactured from its engineering resources (known as the Part Progression) and figures out the transfer sequence, the actual process is pretty straight forward. Wire is drawn into the machine, cut-off, and transferred to the first station. That cut-off blank is then sequentially transferred to each station in the machine until it has seen every tool and drops off as a completed part. At each station along the sequence either one or a combination of the heading processes, upsetting, extrusion, or trimming/piercing, as designed by the engineer and built into the tooling will occur.
Is There a Difference Between a Parts Former and a Nut Former?
Is there a difference between a Parts Former and a Nut Former? The simple answer to this question is yes. Although the processes being performed, upsetting, extrusion, and trimming/piercing are fundamentally the same, the execution and machine parameters are different.
Machine Stroke/Speed:
With every strike of the machine the part is usually forced into the die. The part requires some assistance to be removed from the die. This comes in the form of a pin (known as the Knock Out Pin) which pushes forward all the way to the face of the die as the ram (moving side of the machine) is moving backward. As parts get longer, the effective part of the dies must also get longer resulting in a longer forward stroke of the pin to reach the die face. Obviously the longer the stroke, the more time it takes to accomplish this task and the slower the machine can run.
Machines are designed to optimally run certain lengths of parts and are available in short, medium, and long stroke versions. Naturally a long stroke machine will have the capability of running longer parts while a short stroke machine will be limited to shorter parts. When you consider the design of screws, bolts and nuts, it would be fair to describe most screws and bolts as “long and thin” and most nuts and hollow parts as “short and stubby”. Screws and Bolts, therefore, need machines with medium and long stroke capability while nuts only require short stroke machines. The resulting significance of this is that Nut Formers will run faster than their Parts Former counterparts because it takes less time to push the Knock-Out Pin forward.
Number of Stations:
In theory a Multi-station Former can have an infinite number of stations. In practice, however, the number of stations is limited because too many would result in such a wide machine that it would be impractical for an operator to run it. Therefore, Parts and Nut Formers usually do not exceed about six stations. In fact, more often than not, nuts need more stations than bolts and screws so that a fastener manufacturer specializing in bolts and screws likely has more Four Station Parts Formers than five or six station while nut manufacturers likely have almost all Five and Six Station Nut Formers.
Transfer:
One of the biggest distinguishing factors between Parts and Nut Formers is the method of transfer between stations. When forming a bolt or screw there are two distinct regions of the part, the head and the body. Forming of the head is well suited to the punch side tooling and the body to the die side tooling. In most instances there is no advantage to being able to flip the part around and from an engineering standpoint the “long and thin” aspect ratio would make this difficult or impossible anyway. Therefore, screws and bolts just get transferred straight across.
Nuts, on the other hand, are usually symmetric or nearly symmetric across the center axis. Therefore, if we begin working on one side with the punch, it is likely that working the other side with the punch would be equally advantageous. That is, in fact, the case so that being able to control which side of the part is presented to the punch at each station becomes a strategic benefit. Nut manufacturers therefore, need to find a way to be able to flip the part so that both sides of the part may be strategically presented to the punch or die side of the machine. To accomplish this Nut Formers are equipped with Universal Transfers which unlike the one dimensional transfers of the Parts Former can move the part laterally to the next station or rotate it 180° as it is moved from one station to the other. By flipping the part it allows the manufacturer to work the hole in the nut from both sides of the part, which is advantageous when compared to trying to drive the hole and form the hex shape all from one side.
Summary:
Multi-station Parts and Nut Formers are versatile machines in the manufacturer’s arsenal. They are particularly important in generating more complex net shape parts. Although they provide the same basic functions as simpler machines do, the added stations allow manufacturers to combine functions and make more difficult and complex parts. In particular, Nut Formers are the mainstay of fastener manufacturers focused on nuts and have some unique and special features that provide advantages in nut manufacturing.
multi-station parts former
Laurence Claus
多衝程零件成型機
扣件
國際展會
惠達雜誌
匯達實業
外銷媒合
廣告刊登
螺絲五金
五金工具
紧固件
台灣扣件展
印度新德里螺絲展
越南河內螺絲展
墨西哥瓜達拉哈拉螺絲展
美國拉斯維加斯螺絲暨機械設備展
波蘭克拉科夫螺絲展
義大利米蘭螺絲展
德國司徒加特螺絲展
wire Dusseldorf
FASTENER FAIR INDIA
FASTENER FAIR VIETNAM
FASTENER FAIR MEXICO
FASTENER POLAND
FASTENER FAIR ITALY
FASTENER FAIR GLOBAL
FASTENER WORLD
READ NEXT
2021-11-02

Subscribe
