Industry Activities
Challenging the “Minimum” Limits at the Forefront of “Manufacturing” - Thread Cutting Mills by “NS TOOL”
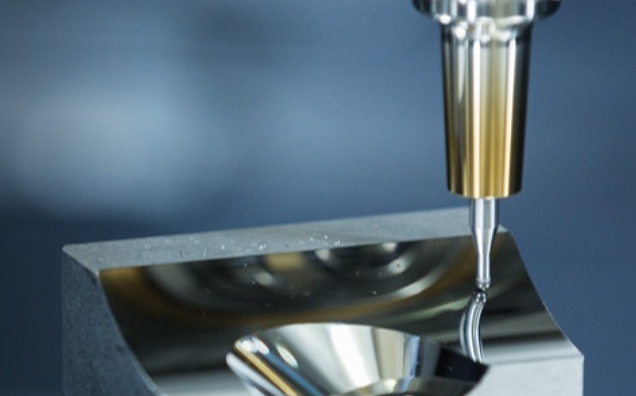
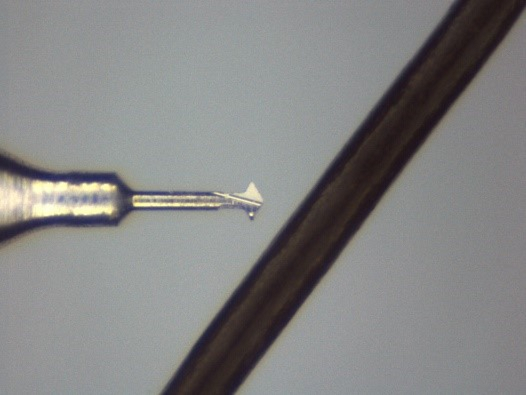

Add to my favorite
2019-12-09
When it comes to thread cutting mill, we must mention the top-notch thread cutting mills from NS TOOL. This Japanese public listed company has been studying and developing solid carbide end mills since it was founded in 1954. It continuously challenges the limits of “minimum diameters”. Using its end mills, you can even produce products so small that are barely visible to the eyes. Therefore, its end mills are highly precise with smaller tolerances than are required by drawings. Now, NS TOOL has become the only major company in Japan that sells end mills of 0.01mm diameter as its standard product. It provides over 9,000 types and has a market share of over 40% in Japan. Fastener World interviewed the company on its thread milling tools infused with exclusive technology.
NS TOOL's Thread Cutting Mills vs.Thread Taps
There are a couple of advantages in choosing thread cutting mills. An average thread tap, once ruptured, tends to clog up the hole and it has to be resolved with a special tool or via EDM. Since thread milling is usually done close to the final phase of production, any failure could lead to the output of defective products. So for starters, unlike taps, thread cutting mills can be easily re-processed even if they rupture, because their diameters are smaller than the hole’s, which makes them easier to be removed. Secondly, end mills mill materials intermittently and are not quite subject to heat influence, so they are perfect for materials that are hard to be machined. Lastly, end mills receive less resistance from materials in milling, so they are suitable for high precision machining and it is easier to dispose of the scrap.
“Unlike most of our counterparts adopting a 3-layer design, our thread cutting mills adopt a single-layer multicuts design putting emphasis on sharpness to achieve highly efficient thread milling. The best thing about a single-layer design is that you get to freely specify a pitch depending on different cut route programming, so the same piece of thread cutting mill can mill not just standard but also fine threads, even client-specified special threads, to increase variety of clients’ own products. Our thread cutting mills can be easily removed when ruptured and prevent producing defective work pieces at the end of production,” said the company.
Top 4 NS TOOL Thread Cutting Mills and Chamfer Cutter: MMTM, MMTS, MMTU, NSCV/ NSCV-M
MMTM (MUGEN-COATING M-Thread Mill) utilizes a multi-cut design. Available in M1-M6, it takes 1 minute and 25 seconds to machine a hole on a 52HRC (hardness) STAVAX die steel, and is perfect for machining metric female threads efficiently. MMTS (MUGEN-COATING Micro Thread Cutting Tool) has the tiniest cut diameter in the world. On titanium materials it can produce threads of 0.1mm diameter and 0.025mm pitch. Available in S0.1-S1.4 sizes, even smaller than S0.3 specified by Japan Industrial Standard, it can produce mini-female threads as thin as a hair. MMTU (MUGEN-COATING PREMIUM Thread Cutting Tool) adopts a cut shape with a focus on sharpness and increases machining precision. Available in No.0-80UNF~1/4-28UNF sizes, it is perfect for machining inch female threads. NSCV/NSCV-M (chamfer cutter) comes with a tough rake angle and great sharpness to ensure the integrity of the machined surface and suppress the occurrence of burrs.
Independent Research and Development of Coatings for End Mills
NS TOOL's “MUGEN-Coating” is an aluminum-titanium coating with a hardness of Hv3,400 and an oxidation temperature of 1,100°C. The “MUGEN-Coating Premium” has higher performance with a hardness of Hv3,600 and an oxidation temperature of 1,300°C. It is perfect for milling high hardness (48~68HRC) materials and pushes tool life to its limit. The MMTM, MMTU and MMTS end mills use those respective coatings developed by NS TOOL. In pursuit of zero-defect quality, the company self-developed “TGM” end mill manufacturing machines. This enables its product sales to spread across 30 countries (accounting for 30% of its revenues), among which the ROC (Taiwan)/Hong Kong/China region takes 40% and 30% for the U.S. and Europe each.
NS TOOL’s Strategy
Next year NS TOOL will attend international machine tool shows in Japan and Taiwan as well as mold and die shows in Shanghai and Shenzhen. It will also hold an “NS TOOL Private Show” at the end of next January. Regarding future strategies, the company said it will “stick with ‘Made-in-Japan’, utilize domestic technologies to expand overseas sales, and facilitate the miniaturization, long life and high efficiency of end mills.” It closed the interview with the following self-description: “NS TOOL is an innovator unlimitedly expanding the dreams of manufacturing and realizing its potential!”
Contact: Mr. Kai-Ping Wang, International Sales Dept.
E-mail: ns442@ns-tool.com
日本日進工具
螺紋铣刀
鋁鈦無限鍍膜
Japan
NS Tool
thread taps
thread cutting mills
扣件
國際展會
惠達雜誌
匯達實業
外銷媒合
廣告刊登
螺絲五金
五金工具
紧固件
台灣扣件展
印度新德里螺絲展
越南河內螺絲展
墨西哥瓜達拉哈拉螺絲展
美國拉斯維加斯螺絲暨機械設備展
波蘭克拉科夫螺絲展
義大利米蘭螺絲展
德國司徒加特螺絲展
wire Dusseldorf
FASTENER FAIR INDIA
FASTENER FAIR VIETNAM
FASTENER FAIR MEXICO
FASTENER POLAND
FASTENER FAIR ITALY
FASTENER FAIR GLOBAL
FASTENER WORLD
READ NEXT

Subscribe
