Plastic Fasteners by Pingood New Trend for Special Applications
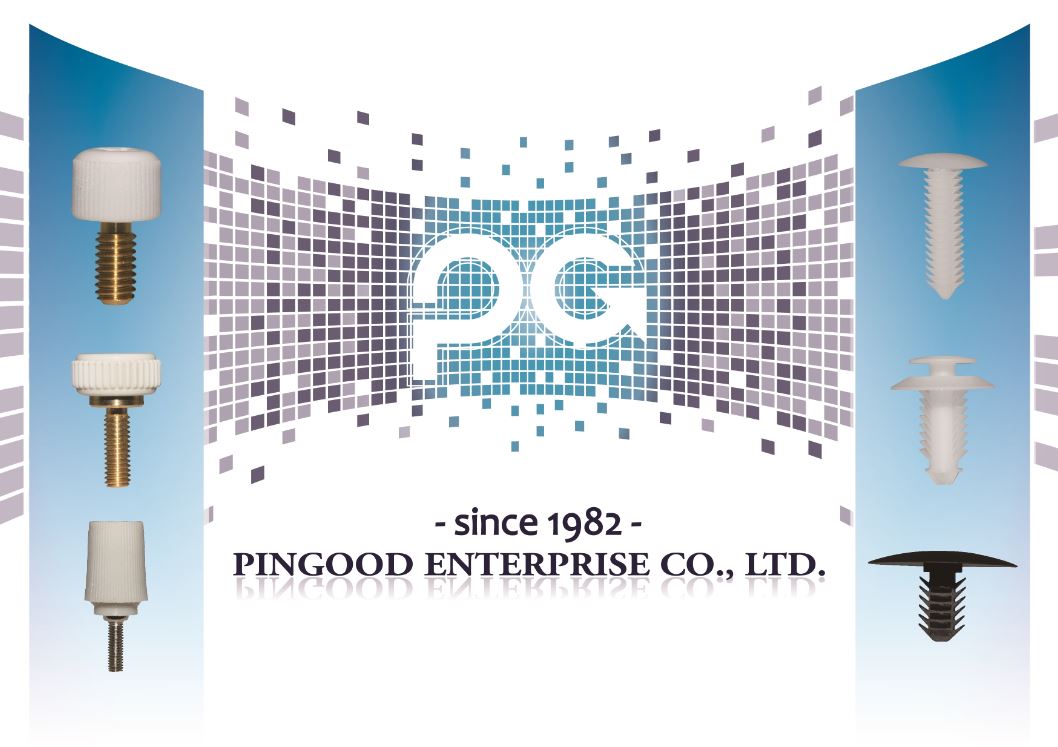

by Finnick Wu, Fastener World
“Sustainable operation, honesty, reliability, and innovation” have been the mission statements of Pingood Enterprise Co., Ltd. for long. Established in 1982 by General Director Lin Mau Shen, Pingood has had over 36 years of experience in fastener manufacturing. Pingood is headquartered in Taipei (Taiwan) and has 3 manufacturing bases in Asia, including one in Chung-li (Taiwan), another in Dongguan (China) and the other in Suzhou (China), among which Dongguan factory spans the largest area of 36,000 sqm compared to the other two factories respectively spanning the area of around 12,000 sqm. In the end of this year Pingood plans to renovate its factories in Chung-li and Dongguan. The renovation will not only include factory expansion and equipment upgrade, but also include systematic integration and introduction of automatic warehouse for transition into Industry 4.0.
The Dongguan factory is equipped with additional molding division with the most sophisticated Japanese machine tools and well-trained mold making engineers to offer vertically integrated service. In order to ensure good product quality, Pingood purchases materials directly from overseas original suppliers and implements strict quality control from material to finished products. In addition to focusing on the sustainable operation in the business, Pingood also recognizes its social responsibility. Through the audit of the most authoritative certification institutes, Pingood has been successfully certified by ISO 9001 in 2003 and ISO 14001 in 2005. Moreover, its products and materials are also compliant with REACH and RoHS standards. Obtaining these international certificates makes Pingood become a brand worthy to be trusted as well.
New Future Trend- Plastic Fasteners
Rather than focusing onmetal fasteners in the market, Pingood has been dedicated to the development of plastic fasteners. The existence of plastic fasteners in the market can be attributed to their special characteristic. Compared to metal fasteners, plastic fasteners with the corrosion-resistant characteristics are oftentimes used in some special equipment (e.g. where there exists chemical substances). Metal parts used in some equipment have to be used with plastic fasteners due to conductivity and influences related to EMR, as a result plastic fasteners still cannot be replaced by metal fasteners in some way. On top of that, with the upcoming trend of IOT, the facilities for WiFi and RF will be used more frequently and the demand for plastic fasteners will be greatly increased as well. Although the strength of plastic fasteners is limited in nature, however, through reinforcing the design, they can be also used in various products.
Superior Internal Structural Parts on Par with Those of Int’l Leading Brands
Main products of Pingood are plastic mechanical fasteners, which are mostly rotary dampers, push latches, bushings, space supports, LED hardware, fasteners, cable managements, plastic feet, circuit board ejectors, PCB guide rails, handles, housings and covers, etc. The excellent quality of rotary dampers and push latches are particularly worth mentioning and is on par with that of European, US and Japanese products. The rotary dampers and push latches can be used on any panels that require “push to open.” The panel can be opened/closed with just one push on the latch and can be slowly opened and closed with the support of rotary dampers, enhancing the performance of quality but also increase the durability for product.
Introducing Electric Injection Molding Machines, Increasing Capacity and Ensuring Quality
In terms of market changes, Pingood says that the industry is currently facing challenges like small-volume and large-variety production and customization. In addition, requests for more sophisticated products, shorter product life cycles and how to meet customers’ needs in time as well as calculate the inventory turnover and offer more efficient production have all become issues companies involved have to deal with. Facing such challenges, Pingood also has its own countermeasures. Since 2014, it has started to replace the old machine tools with new ones. Thus far, around 70% of the injection molding machines in its factories have been replaced with Japanese TOYO, FANUC CNC, SeiBu WEDM and Sodick EDM. For reducing electricity loss and add extra capacity, the newly installed machine tools are all electric, which reduces the demand for labor force. The molds used also passed strict quality control, which guarantees the safety of products. On the other hand, in order to protect the environment, save energy and reduce carbon emission, Pingood’s factory in Dongguan has been also installed with solar panels, which can save carbon footprints equivalent to planting 800 trees every year and fulfil its responsibility as a global citizen.
R&D Focus in 2019- Tiny Molds and Green Energy Industry
The R&D focus of Pingood in 2019 will beonproducts that are smaller/thinner and of the same strength, in order to correspond to the increasing demand for lighter, thinner and smaller items. In addition, it will also add some UV resistant ingredients into products to increase the strength and product life cycle, making them better suit to be used in outdoor facilities like solar panels and telecommunication. Through different compositions of materials, durability and strength of products can be enhanced, flexibility in design can be improved, and assembly and labor costs can be reduced.
Pingood contact: SALES REPRESENTATIVE
Email: sales@pingood.com.tw

Subscribe
