
Industry Activities
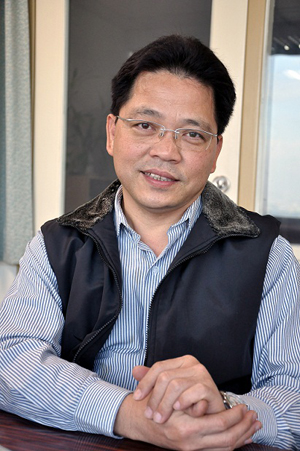

by Kelly Wang, Fastener World
Small-size hardware commodities comprise many types and are small. Therefore, taking stock of them often gives a stock taker a headache. If there is a shortage or a surplus in the stock, this would be a problem and a nuisance to the management level. Taking stock again is quite time-consuming and labor-consuming. What went wrong? Was it the relevant workers? Was it the procedure? Or was it because the stock management system was not properly used? How can we take stock of small-size hardware commodities effectively? What is the right inventory management system we should choose? We interviewed several manufacturers of small-size hardware commodities (specializing in the manufacturing of screws, nuts, electronics screws, iron-zinc alloy pipes, different types of accessories/fixtures and iron pipes) and a company specializing in inventory management systems, and we would like to share the secrets in the stock taking of small-size hardware commodities with you.
We have interviewed several manufacturers of small-size hardware commodities to understand how they take stock. Larger manufacturers would set up a schedule, choose a suitable inventory management system and train their warehouse persons. Smaller manufacturers use experienced workers to take stock and record data in statistical software such as Excel. In fact, each manufacturer has its own particular needs and it is not necessary for each manufacturer to purchase inventory management software. Each manufacturer should adopt a stock-taking system or method suitable for itself to effectively control production, cost and stock. The aim is to control stock as the sales figure goes up.
A. If the stock management of small-size hardware commodities has been a mess and many commodities do not have a product number tag, how do we take stock?
1. First, establish a procedure of stock management. For examples, who is in charge of the stock window? Who is in charge of taking stock on a daily or periodical basis? Who is in charge of recording? Who is in charge of checking inventory?
2. When commodities go out, the quantity and the remaining quantity should be entered into a merchandise outgoing slip. When you take stock, an inventory detailing the types and their quantities should be printed out. Then assign people to take stock.
3. If the product number of a certain type of commodity is erroneous or can not be traced, you should use a pen with a different color to enter the name and product number to highlight it.
B. Matters that should be aware of before and after you take stock
1. You should establish measures against theft, measures to prevent commodities from damages and a procedure to handle damaged or soiled goods. Before your company takes stock, you should plan out how you will do it (including methods, goals and the selection of persons) and every member of your company should be involved in the matter. In our interview with Mr. Guan-Chun Wu, who is the president of Le Yiao Enterprise, he expresses: a company should train each member to be able to take stock and each member should be responsible for stock taking, so that each step of it may be correctly carried out.
2. After you take stock, a complete inventory and reports on types of goods that are low on stock and the changes of certain types of goods on the stock should be printed out. If necessary, you should use different types of graphs or charts (such as run chart, pie chart and bar chart) to demonstrate the fluctuation over the years, so that others may understand it swiftly. In addition, the stock condition should be updated on a constant basis, so that stock may be managed efficiently. Also, the causes for damaged goods and how damaged goods are handled should be clearly recorded.
※ The following are some suggestions given by Mr. Sheng-Zhe Chu, the project manager of ADEN Information Ltd.
Q: What are the problems in the stock taking of hardware commodities? In the designing of an inventory management system, are these problems taken into consideration?
A: The biggest problem in business operation facing the hardware trade is the number of the types of commodities and each type of commodity has its own specifications. In addition, each type may be further divided into several grades or classifications and each classification may have its own discount percentage. Therefore, a lot of time is wasted in ordering commodities, sale and checking/taking stock. Taking stock is particularly so. If you do not have an inventory management system, you would need to put in a lot of effort just to establish inventory. As of now, inventory management system has many powerful functions, such as basic data of commodities (according to their classifications), basic data of clients (according to their classifications) and final selling prices of commodities (with the adjusting function). If any of small-size hardware manufacturers would like to try out such inventory management system, please log onto the official website of ADEN Information Ltd. (http://www.aden.com.tw) to download the free trial version of the system.
Q: When we use such small hardware inventory management system, would you give us any tips to reach the goals of correct entry of data and the reduction of manpower and time? Is there anything that we should be aware of when we use such a system?
A: The most important thing in using any information system is data are correctly input into the system. Though the system has certain mechanism to prevent incorrect entries, the system can not determine the correctness of an amount or a quantity. Therefore, incorrect data entries often occur due to human negligence. For example, commodities of a shipping order or commodities returned to other company are not deducted from the stock; commodities ordered by your company or commodities returned to your company are not added to the stock. In addition, you should pay attention to details. For example, if a box contained 10 pieces of merchandise before (when your client ordered the merchandise) and, now, a box only contains 8 pieces, you should be careful when such merchandise is returned to your company from your client because there should be 10 pieces in each box, instead of 8 pieces.
Q: According to your long-term observation, what is the percentage of the companies in the small hardware trade that have adopted a computer aided inventory management system? Do you have any suggestion for the companies in the trade that have not adopted such system? What are the benefits of such a system?
A: As of now, only a small portion of the companies in the relevant trades of Taiwan use such a computer aided system to carry out their inventory management. Though the government has been promoting the use of computers and some companies have started to use it, most of the small-size and mid-size companies have not adopted such a computer aided inventory management system. This is particularly so in the southern region of Taiwan. After all, old habits and practices die hard. Nevertheless, the relevant companies should try out this system in order to enhance the efficiency in inventory management and to save time and manpower. If they can find the right system and system provider, the goal of effective inventory management may be reached.

Subscribe
