The Fastener Supplier for the Largest Aircraft Engine Manufacturer GE--NAFCO: Every Screw Shows Our Promise and Responsibility to Passengers On Board
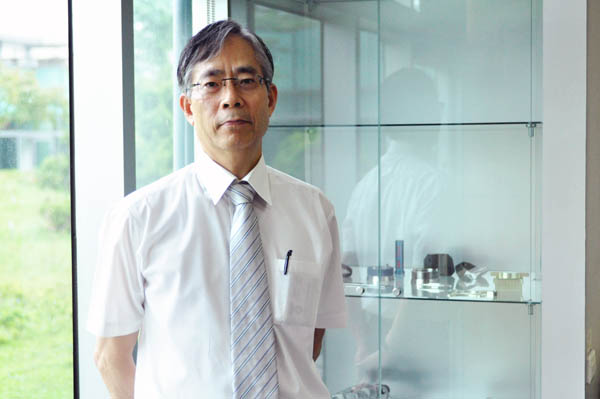
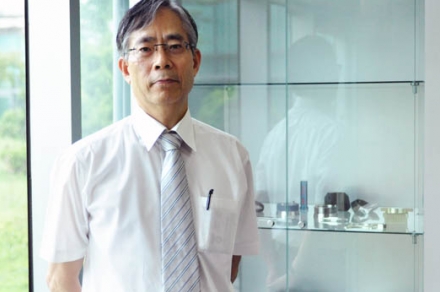
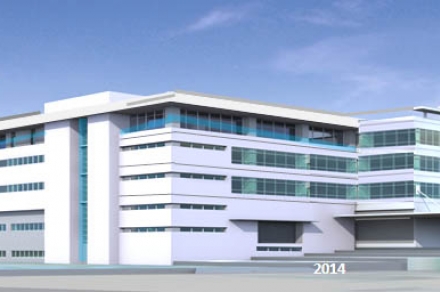
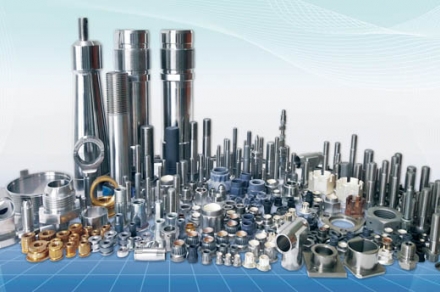
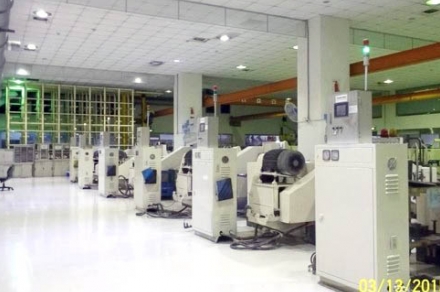

The Pingzhen, Taoyuan-based National Aerospace Fasteners Corporation (NAFCO) established in 1997 is a manufacturer of aerospace fasteners. NAFCO was established by the technical team of AVIBANK (one of the 3 largest U.S. aerospace fastener manufacturers at that time) and the monitor manufacturer Royal Information. NAFCO is the only GE approved aerospace fastener supplier in Asia Pacific. It has complete manufacturing procedures for products with very high entry barriers for other competitors. Moreover, NAFCO has been recently approved by the German aircraft engine manufacturer MTU, which opens a new chapter for the development of aerospace fasteners in Taiwan.
With a Specific Target to Take the Lead in the Aerospace Industry
NAFCO’s plant in Pingzhen, Taoyuan looks more like an IT company with clean windows and tidy offices rather than a traditional fastener factory. On the 3 plant areas of over 26,446 sqm, NAFCO manufactures various aerospace fasteners. NAFCO Vice President Mr. Chiu said that since the inception of NAFCO in 1997, the word “aerospace” has been included in the company name to show its main business direction.
The products of NAFCO are applied to aircraft engines and motor vehicles. Major products are Ni-alloy engine nuts and bolts, as well as machined parts and industrial & automotive parts. 99% of its products are for export to America, Europe and Asia. America represents 70% of its sales, Europe represents 19%, and Asia represents 8.8%. Its largest client is a U.S. aerospace engine manufacturer. Vice President Chiu added, “Asia has just begun its development of aerospace fasteners; however, European and U.S. suppliers have been dedicated to the R&D and production in this field for 4-5 decades. Many Asian suppliers are still far behind these companies in terms of technology. Fortunately, the supply chain of Taiwanese fastener industry is well-established, which is favorable to the development of the company.”
Sophisticated Processes Under Strict Surveillance
Vice President Chiu seriously said, “Engines are the most important large parts of the entire aircraft. Fasteners installed on aircraft engines must be able to withstand temperatures of more than 1,000 ℃ and resist high torque values. The procedure of manufacturing an aerospace fastener includes at least 20 steps (e.g., design, material selection, temperature control, heat treatment, etc). If it is an automotive fastener, it can be finished within only 7-8 steps. As a result, every step and every part must be inspected separately, because the requirement for safety coefficient is very strict.”
The safety of any products from NAFCO is very critical to applications, so NAFCO has recruited a team of experts for aerospace quality control, R&D, and manufacturing technology from domestic and foreign well-known high-tech and research centers. Vice President Chiu thinks, “It is our responsibility to ensure the safety of any plane installed with our products and it is also our commitment to our clients.” Such a serious and careful attitude is held at all times by 370 NAFCO employees.
Requirements for Excellent Quality and Recognition from International Leading Companies
NAFCO was respectively certified by GE in 2001 and Snecma (of Safran) in 2003, making it the 1st approved aerospace engine fastener manufacturer in Asia Pacific. Years later, it successfully entered the supply chain of many well-known companies (e.g., AVIO, AVIALL, IHI, SAMSUNG, EATON, FAURECIA, INFASTECH, MOOG, Triumph UK/YAK, Messier-Bugatti-Dowty, etc). Vice President said straight, “Our competitors have begun investment in R&D for more than 50 years, so we have to work really hard before we can gain a presence in the aerospace fastener industry.”
In 1998, NAFCO was certified to ISO 9001. Later in 2004, it introduced the AS 9100 quality management system and was approved by NADCAP and many clients’ special manufacturing procedures standards. In addition, its metal testing lab was also approved by clients’ S400 and FAL448 standards. The quality management system of NAFCO is always customer-oriented. In order to satisfy clients’ increasing demand, NAFCO is planning to set up its 4th plant in Taoyuan.
As Boeing and Airbus still have many unprocessed orders, it is expected that many aircrafts will be delivered to clients in the following few years. Moreover, with the growing low-cost carriers market in Asia Pacific, the next-generation engines are also very likely to bring new growth momentum. Vice President Chiu said firmly, “Passion, honesty, and integrity are our operation principles. Only with these principles can NAFCO become a leading aerospace fastener supplier with high efficiency and continuous growth.”

Subscribe
